As every business owner or manager knows, there’s one crucial facet of developing an optimized supply chain: warehouse management. From inventory control to order fulfillment, an effective and organized system maximizes revenue flow and ensures operations run as smoothly as possible. Implementing best practices for storing, packaging, and shipping your products can help drive repeat business and minimize costly errors. By following these tips and tricks, you can ensure your warehousing operations are moving seamlessly – thereby meeting your customers' needs.
Inventory Tracking
Inventory management is a crucial piece of tracking everything from order placements and product levels to sales and deliveries. Just think of it from the consumer perspective – things like stockouts or deliveries arriving late can truly hinder your brand’s reputation and eat away at your customer lifetime value. By implementing an inventory tracking strategy, you can maximize space utilization, monitor inventory levels, reduce overhead costs, and improve customer service.
What’s more, inventory tracking ensures all key stakeholders in the supply chain have access to timely and accurate information surrounding your products. Leveraging a warehouse management system (WMS) is an effective way to keep tabs on both inventory levels and product movement through the warehousing stage.
The right WMS will use automation and technology, like RFID readers or barcode scanners, to facilitate product movement and storage. The benefits? Improve inventory accuracy, identify and resolve bottlenecks, and decrease stockouts. Real-time inventory level visibility allows your business to improve decision-making processes and, ultimately, customer service.
Harnessing Automation
Here’s the reality: manual processes are outdated. Incorporating automation into your warehousing best practices is vital for improving efficiency, decreasing costs, and increasing accuracy. When automation is woven into your strategy, it can help streamline workflow, including picking/packing, shipping, and inventory tracking.
What’s more, automation has the power to minimize human error and speed up the entire order fulfillment process. Think about it: every stage of the process – picking, packing, shipping, return management – can all become more efficient when data is collected and digested using automation. With technology serving as a fundamental part of conducting business in today’s competitive landscape, companies simply cannot afford to leave it out of their warehousing strategy.
Putting Warehouse KPIs in Place
How can you measure the efficacy of your warehousing operations? Through the use of key performance indicators (KPIs). KPIs allow business leaders to evaluate performance, identify improvement areas, and implement changes to their processes. These metrics can truly help businesses scale and drive long-term success, simply by providing visibility into their operations.
Here are some of the most common KPIs used to measure and improve warehousing procedures:
- Order fulfillment accuracy – used to measure the percentage of orders that are fulfilled accurately.
- Inventory turnover – used to assess the rate at which inventory is being sold, processed, and replenished.
- Order lifecycle – used to measure the average time required to complete an order from placement to delivery.
- On-time delivery – used to measure the percentage of orders delivered on time to customers.
- Quality control – used to measure product quality (a KPI that’s particularly important for cold chain products).
- Shipping cost – used to measure costs associated with shipping goods to customers.
- Warehouse utilization – used to measure the amount of space your inventory is consuming and if it’s being used effectively.
Identifying the Right Warehouse Management System (WMS)
With the right WMS on your side, you’ll have the ability to optimize everything from storage and retrieval to tracking and shipping of your merchandise. Investing in a technology-driven WMS can provide a whirlwind of benefits for your business, like reducing costs, streamlining operations, and elevating customer service. The right WMS will also be equipped with the ability to decrease costly errors by improving order accuracy and adequately managing stock levels.
So, what type of features should you look for? Here are the key elements to consider when identifying a WMS that’ll help you achieve your business goals:
- Scalability: As the needs of your business grow and change, you’ll need a WMS that has the ability to effortlessly scale with you. It should have the functionality required to accommodate things like having a presence in new marketplaces or expanding product lines.
- Productivity: The right WMS can play an integral role in driving operational efficiency. It should be equipped with features such as automated data capture, inventory tracking and replenishment, order picking and packing, and order tracking.
- Integration: In order to keep operations flowing seamlessly, you’ll want a WMS that can easily integrate with your technology stack – i.e. your customer relationship management (CRM) and enterprise resource planning (ERP) systems.
- Reporting: Getting the most out of your WMS means having access to analytics and reporting tools. Having this data will enable your business to gain crucial insights into your warehousing operations and make data-backed decisions based on your findings.
Warehousing Best Practices to Fuel Your Success
In today’s increasingly competitive business world, your success relies on optimizing your warehousing operations. Implementing warehousing best practices and having a forward-thinking strategy in place can provide the competitive edge your business needs to come out on top. When you partner with a logistics and fulfillment company like Smart Warehousing, we’ll do all the heavy lifting for you. Our goal is to help streamline warehousing processes and increase efficiency across your supply chain to improve your bottom line.
Discover how Smart Warehousing can take your business to new heights by contacting us today.
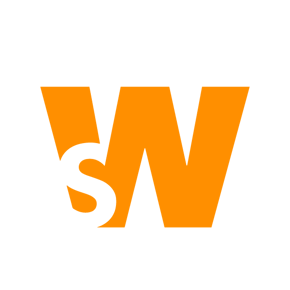