Though they sound straightforward, the three words “pick, pack, ship” play a significant role in the success of your company’s logistics operations. Pick, pack, ship, when done right, ensures a streamlined order fulfillment process, leading to satisfied customers receiving their ordered items on time and your company standing out from your competitors.
So what exactly is pick, pack, ship? Essentially, it’s the process of selecting recently purchased items from inventory in the warehouse, packaging them into boxes, and shipping them to the customer. However, some important best practices and strategies must be implemented at every order fulfillment stage to ensure your pick, pack, ship process is effective enough to keep up with consumer demand.
Implement These Key Pick, Pack, Ship Best Practices into Your Logistics Operations
Pick
At first glance, finding and picking inventory off of shelves sounds like an easy task. But it quickly becomes complex when you have a warehouse full of inventory that spans several acres—and thousands of orders to fulfill. As a result, experienced fulfillment teams will utilize different picking strategies as part of their pick, pack, ship process to obtain items more efficiently, such as:
- Zone Picking - dividing your warehouse into specific zones and assigning pickers to manage each zone
- Batch Picking - collecting items for multiple orders at the same time to reduce the amount of trips and time spent locating items
- Wave Picking - collecting a set amount of orders during specific intervals of time, allowing pickers to rotate through larger amounts of orders
It’s important to incorporate reliable warehouse management software (WMS), like Smart Warehousing’s SWIMS system, into your operations. A quality WMS will make tracking and managing your inventory easier, streamlining the pick, pack, ship process. Mobile barcode scanners integrated with your WMS are also helpful for pickers to quickly locate inventory.
As you receive inventory and organize your warehouse, keeping your pickers in mind will boost your picking efficiency as well. Providing detailed warehouse maps that indicate where inventory categories are stored with designated picking routes shortens walking time. You can even store more popular inventory in central locations. Supplying your pickers with tools that help them do their jobs more easily, such as containers, pallets, and carts, should be your priority as well.
Pack
Once you pick your orders, it’s time to pack them so they can be shipped. To start, you need to ensure your packers have access to quality packing supplies so your orders can be packed correctly (helping you cut down on transit damage). In addition to utilizing cardboard and plastic boxes, you want to use dunnage like bubble wrap, kraft paper, and air pillows. You can even consider box alternatives like polybags to reduce shipping costs.
Another key step in the pick, pack, ship process is including a packing slip for each order. A packing slip helps your packers determine what should be packed for every order (and is typically included in the box when the customer receives it). Each packing slip should feature details like:
- SKU numbers
- Item list and quantities
- Customer’s contact information
- Out-of-stock items ordered (but not fulfilled)
Ship
There are various strategies to make the shipping aspect of your pick, pack, ship operation timely and cost-effective. If certain inventory items are frequently ordered together, you can consider kitting these items into one SKU and marketing this kit as a new product, reducing shipping costs by sending them all at once.
It’s a good idea to calculate your shipping costs beforehand when orders are placed to avoid any unexpected charges. Knowing what to expect with shipping costs will give you and the customer peace of mind. You can calculate shipping costs in advance by factoring in box dimensions, weight, item value, and priority shipping level.
Another best practice to consider is utilizing multi-location fulfillment centers. Rather than having one main warehouse to fulfill your orders nationwide (or globally), fulfilling orders from multiple locations gives you several benefits. Not only can your company lower its shipping costs, you can also speed up delivery times and increase your order capacity while protecting your pick, pack, ship process from unexpected weather delays.
The Right 3PL Makes Pick, Pack, Ship Easy
When it comes to pick, pack, ship, perhaps the most advantageous best practice is to partner with a 3PL to manage the entire process. With a trusted 3PL taking care of your logistics, it’s easy not only to keep up with your fulfillment needs, but also to focus on other priorities of your business.
At Smart Warehousing, our expertise as a 3PL goes beyond pick, pack, ship to replenishment, inventory management technology, transportation, and more. If you’re ready for a reliable single-source experience for all your logistics needs, contact us today to get started.
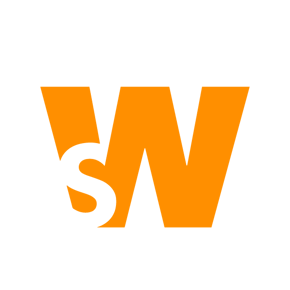