Inventory replenishment is essential to any e-commerce, retail, or fulfillment-based business. Why? It guarantees you restock your products regularly to maintain access to the right items at the right time within your warehouse. With proper inventory replenishment practices in place, your shipping times and customer satisfaction will improve, eliminating significant pain points in your supply chain.
What is Inventory Replenishment?
Replenishment means moving inventory through the supply chain to account for demand. It is an essential part of a successful inventory management strategy, as inventory that needs to be replenished cannot be managed efficiently.
The inventory replenishment process can vary depending on your unique business and fulfillment set-up. For example, an e-commerce business may replenish product by ordering more from their manufacturer or supplier when certain items run low. Large companies may have reserve storage for slow-moving inventory, which will then be used to replenish their main fulfillment center as needed.
How Does Inventory Replenishment Work?
As simple as it is to define replenishment, the act of replenishing is very complex and involves a lot of logistical elements to get right. Let’s dive in.
Replenishment Amount
Replenishment requires accurate demand planning, using logistics and forecasting to anticipate the amount of inventory needing replenishment at any given time. On the flip side, inventory replenishment requires knowledge of when not to replenish to avoid overstocking, especially with limited warehouse space. Especially for businesses selling seasonal items or with demand fluctuation, having the right quantity at the right time is crucial. Snow boots aren’t exactly in demand in July, for example!
Replenishment Lead Time
It’s also important to know the lead time—how long it takes to receive inventory and have it ready to use after ordering it—for effective inventory replenishment. Think of it like empty shelves in a grocery store. If the store owner waited until a shelf was empty to contact their supplier, the shelves would not be instantly replenished. They would remain empty throughout the lead time, frustrating customers who cannot access the groceries they need. Just remember how annoyed you were the last time your supermarket was out of your favorite item: it’s easy to see why this can be harmful for your brand.
Predictive Analytics
To properly manage replenishment amounts and lead times, predictive analytics are vital in forecasting inventory needs. It can be hard to fully anticipate inventory needs in advance, but predictive analytics use historical data and market trends to estimate future demand, allowing you to schedule replenishment in advance and reduce the risk of going out of stock while waiting on extensive lead times.
Inventory Capacity
Replenishment is heavily reliant on your capacity. If you have limited warehouse space, this limits how much stock you can have in your fulfillment center waiting to ship. The smaller your capacity, the more important it is to have a streamlined inventory replenishment strategy to keep your stock always on the move.
Product Shelf Life
If your business is part of a cold chain or otherwise manages products with a limited shelf life, inventory replenishment becomes even more nuanced. You need to know exactly how much product moves regularly out of your fulfillment center to your customers so your stock won’t expire while sitting stagnant in a warehouse.
Why Does Inventory Replenishment Matter?
Healthy inventory replenishment processes are important for the greater health of every business. Effective stock replenishment strategies can support your business by:
- Helping you avoid stockouts
- Reducing the risk of overstocking
- Improving customer satisfaction
- Increasing visibility
- And decreasing shipping costs
Tips for Effective Inventory Replenishment
Want to go the extra mile with your inventory replenishment strategy? Here are a few ways you can aid replenishment in creating a seamless fulfillment experience for your customers:
Optimize Your Warehouse
Inventory efficiency is heavily dependent on warehouse organization. This doesn’t just mean having enough space to keep your stock tidy—it also means strategically placing inventory to flow in and out of your warehouse in the most effective manner possible. Fast-moving inventory should be placed toward the front of the warehouse and on easily-accessible shelves, as this will also make constant replenishment easier.
Increase Visibility
Literal visibility of your products is one thing, but you also need to have good visibility of the journey your products take from the manufacturer to the customer’s front porch. The most optimized inventory visibility allows you to know where each product is in its journey through the fulfillment process. Inventory replenishment relies on providing accurate and real-time data to your suppliers, so they always are informed when stock levels are low.
Partner with a 3PL
This final tip is the real crux of the issue, as it will help resolve all other aspects of inventory replenishment. The right third-party logistics provider can bring you and your suppliers powerful forecasting, real-time warehouse and inventory data, and fulfillment that is optimized for your business’s needs.
Replenish Your Inventory the SMART Way
With our Smart Replenishment program, your brand will be empowered through meticulous data, last-mile delivery support, significantly reduced damages and capacity issues, and, of course, top-tier shipping for all of your customers. We help you maintain visibility control of your inventory through seamless integrations to improve your margin and let you focus on your core business.
Are you ready to experience the difference Smart Warehousing can make for your business? Reach out to learn more.
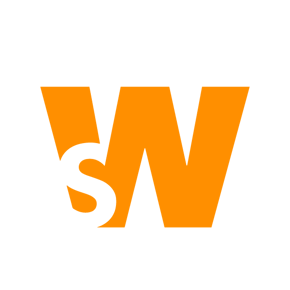