Inventory Information Is Inaccurate
Inaccurate or outdated inventory data is an obstacle to maintaining efficient warehouse operations. Pickers waste time searching for missing items, leading to delayed orders and a poor customer experience. According to Honeywell, warehouse picking errors can cost a business anywhere from $10 to $250 per mistake!
Inaccurate inventory data can also lead to:
- Overstocking and Understocking: Without clear visibility, you might end up with too much of the wrong item (wasting space and dollars) or not enough of the right one (leading to backorders).
- Dead Stock: Inaccurate data can hide forgotten inventory that becomes obsolete, tying up valuable warehouse space and eating into your profits.
A Warehouse Management System (WMS) serves as a centralized database, keeping operations running smoothly. It integrates with barcode scanners to capture real-time inventory data, eliminating the need for manual updates and guesswork. Regular system audits ensure your physical inventory matches your digital records, preventing discrepancies that cause picking errors.
Warehouse Picking Routes Aren’t Optimized
Are your warehouse workers spending half their shift just walking between picking locations? Sounds less-than-ideal to us. This inefficiency can eat away at profits and create dissatisfied customers. Without optimized warehouse picking paths, pickers can become fatigued, leading to errors that cause order returns, delays, and lost sales.
Partnering with a 3PL that uses smart WMS can completely transform your warehouse picking process. A WMS can analyze your warehouse layout, inventory placement, and order data to create optimized routes. This, combined with dynamic picking methods like zone picking, batch picking, and wave picking, can decrease travel times and improve warehouse picking rates. The result? Happy pickers, satisfied customers, and a healthier bottom line.
Human Error Is Impacting Your Success
Even the most meticulous picker can grab the wrong item, miss a quantity, or struggle with inefficient processes. Every warehouse picking mistake chips away at your bottom line. Unchecked errors lead to missed fulfillment targets, rising operating costs, and a surge in customer returns.
With a WMS, you can reduce human error and equip your pickers with real-time order data. Technology like barcode scanners allow pickers to instantly access and verify information for each item, boosting both accuracy and confidence.
Lack of Visibility in Picking Process
Relying on manual warehouse picking creates information silos and provides no visibility into the efficacy of your processes. Mistakes can fly under the radar at any point, as there’s no effective way to track them. Paper trails can't track key metrics like picker efficiency, inventory levels, and picking activity. Without real-time data and visibility into KPIs, optimizing your picking process and identifying improvement areas are virtually impossible.
By utilizing a WMS, however, you’ll be able to analyze information from various sources to track picking rates, accuracy, order completion times, and ongoing activities. You’ll also gain real-time insights into open orders, picked items, and pending inventory. These insights are pivotal, allowing you to monitor order progress and address picking challenges as they arise. With this improved visibility comes the ability to access accurate stock counts, predict demand fluctuations, and identify potential shortages before they disrupt your operation.
Inability to Scale with Demand
Holidays and discount sales are golden opportunities for your business to increase revenue, but can your warehouse picking keep up? Inflexible picking processes can slow you down during periods of high demand, leading to delayed deliveries and unhappy customers. The inability to handle seasonality or a sudden influx of orders can truly damage your brand’s reputation..
The way to effectively drive scalability? Utilize a warehouse management system. A WMS can:
- Provide data-driven insights to streamline tasks, optimize routes, and recommend best picking methods as order volumes surge.
- Leverage automation to support your warehouse picking during peak demand.
- Predict future demand by analyzing historical trends and identifying demand patterns.
The Future Is Smart & Streamlined
Traditional warehouses are struggling to keep up with the ever-growing demands of omnichannel fulfillment. Enter: the smart warehouse—a game-changer for everything from order fulfillment to warehouse picking. By leveraging technology, you can gain crucial insights into every corner of your operation, allowing you to optimize processes and improve efficiency.
At Smart Warehousing, we leverage cutting-edge technology to strengthen your supply chain and boost the long-term success of your logistics. Contact our team to discover how we can tailor a solution to fit your unique business needs.
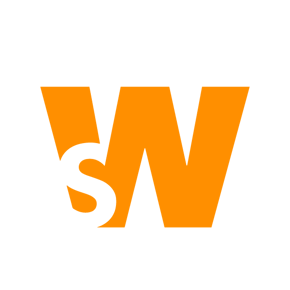