At the epicenter of business growth and operational efficiency is the ability to maintain accurate inventory figures. Because let’s face it: the repercussions of inaccurate stock levels stem far beyond the loss of just a single customer or sale. It can negatively impact your company’s reputation, causing long-term damages. There’s no denying the significance customer reviews play in the consumer decision-making process. The takeaway? Getting it right is imperative.
From establishing sales trends to uncovering discrepancies in inventory numbers, implementing a strong inventory counting process will decrease costs, successfully meet consumer demand, and increase profitability. The most popular method for inventory today? Meet cycle counting.
What Is Cycle Counting?
Cycle counting is a technique used to ensure your company’s physical inventory aligns with your inventory records. This method requires regular inventory counting to reveal inaccuracies and document specific product adjustments if needed. Supply chain specialists and warehouse managers typically oversee the execution of the cycle counting process, devising a strategic plan of action for auditing inventory.
To achieve high stock record accuracy and minimal transaction error rates, you’ll need to implement an inventory management plan that focuses efficiency. Without a well-crafted strategy, the process will weaken productivity and take workers away from completing more high-level initiatives. Whether you opt to utilize perpetual or periodic inventory practices to track product stock, adhering to a regular cycle counting schedule is an essential piece of your overall supply chain management strategy.
Physical Inventory vs. Cycle Counting: What’s the Difference?
A physical inventory count is a carefully coordinated process in which personnel manually count merchandise and compare it against company records. Performed once or twice a year — typically at the close of a reporting period — a physical inventory count often requires a temporary shutdown of operations to stop the movement of product while a full-scale tally of all available stock is documented. There’s no sugarcoating it: physical inventory is a huge undertaking. Plus, it’s not always feasible. A physical inventory count is typically effective only for smaller businesses with minimal inventory.
Cycle counting, on the other hand, breaks the counting process down into manageable chunks by counting small, predetermined batches of inventory multiple times throughout the year. By doing so, businesses can extrapolate data accumulated over time to generate a more accurate picture of their entire inventory.
If your cycle counts repeatedly expose inventory discrepancies, performing a complete physical inventory count is a valuable way to ascertain where your actual stock levels lie. Similarly, if your business has yet to introduce a cycle counting policy, consider conducting a physical inventory audit to establish a strong foundation and ensure you’re collecting quality data.
What makes cycle counting so advantageous? Compared with a physical count, cycle counting conserves valuable time, bolsters inventory accuracy, and ensures reliable product delivery. Many companies choose to perform cycle counting, as well as an annual physical count, in an effort to take a robust approach to inventory management.
Different Cycle Counting Methods
The primary techniques for cycle counting are based on sales ranking or physical area. Leveraging physical area counting means analyzing high-volume goods more frequently. The sales ranking approach, which uses the Pareto Principle, requires auditing the faster-moving, pricier products more frequently.
Also referred to as ABC cycle counting, the Pareto Principle applied to cycle counting assumes that 20% of the parts in a warehouse generate 80% of the sales. (You know, the 80/20 rule.) These are your “A” items: your most valuable products or your quickest-moving SKUs. When extending the principle to your other merchandise, the “B” items represent 30% of the inventory and 15% of sales, while “C” items account for 50% of your warehouse goods and 5% of sales.
Integrating technology, like inventory control software, into the equation will help categorize counted products as A, B, or C items. Logistically, it’s smart to apply cycle counting procedures to “A” items more frequently than your “B” or “C” products.
You can also utilize other metrics, such as production numbers or transactions, to inform your ABC cycle counting strategy. While there are a number of key performance indicators (KPIs) that can provide valuable insight — especially in terms of which products are yielding the greatest impact on overall inventory costs — the majority of software systems rely on ABC cycle counting regardless of metrics used to determine A, B, and C items. Some additional methods of cycle counting include:
- Control Group: This technique focuses on frequent and routine counting of a small batch of items within a short timeframe. It’s often utilized to identify any errors in counting tactics, so they can be rectified moving forward.
- Usage-Based Counting: This tactic counts inventory items that are used most frequently. Each time a product is added or removed from stock, it can initiate inventory variance.
- Randomized Batches: This process encompasses counting a randomly selected batch of items. The number of products to count should be predetermined, and the count can be performed daily to accommodate a large portion of your warehouse inventory within a reasonable period of time.
- Opportunity-Based: This form of cycle counting leverages crucial phases along the inventory management lifecycle, like when an item is ordered, to trigger the counting process. These inventory audits are typically exception-based (i.e., if short–picks occur or stock dips below a predetermined threshold).
- Surface Area Objective Counts: Regardless of inventory value, crews parse the storage space into small-scale audit areas. Workers are responsible only for counting goods that fall within their allotted space on the warehouse map.
- Hybrid Approach: Every business should engineer its own strategy for cycle counting. Think about it — customizing practices to align with your company’s distinct needs and goals will bolster the efficacy of your inventory initiatives. Hybrid plans commonly use the Pareto frequency analysis as a starting point, adjusting their strategy based on data procured and subsequent needs.
Benefits of Inventory Cycle Counting
Even with an optimal tracking, replenishment, and management system in place, companies must still perform routine evaluations of their inventory levels to account for key items. Maintaining inventory accuracy can effectively lower overhead costs and reduce the need for large quantities of safety stock. Why? Because it doesn’t require a full-scale suspension of operations to perform a count of your entire inventory in one shot.
So, it should come as no surprise that cycle counting has taken center stage as a popular inventory management strategy for businesses across sectors. In addition to driving workflow and production stability for your supply chain, cycle counting also includes the following benefits:
- Increased sales revenue
- Reduced errors
- Elevated order fulfillment rates
- Increased accuracy of inventory assessments
- Enhanced customer service levels
- Improved operational efficiency
- Expanded time frame between physical counts
- Decreased audit expenses
- Reduced or eliminated employee overtime costs
- Decreased inventory write-offs and obsolete inventory
- Improved detection of unwanted thefts
- Improved closing process
Cycle Counting Best Practices
For maximum impact, your inventory auditing policy should be systematic and standardized (Read: treat cycle counting like it’s a regular part of business operations). This includes determining the precise intervals in which counting will be performed based on your inventory’s unique needs.
Here’s the reality: inventory is the lifeblood of your business! To drive efficiency, minimize storage costs, and ensure you’re adequately meeting consumer demand, here are some cycle counting best practices to consider:
- Using the ABC method? Establish documented guidelines to maintain classification consistency for each product’s respective counting group.
- Before a cycle count, close all transactions for inventory items to minimize the risk of inaccuracy.
- Determine what to count and the accompanying timeframes of each count. For instance, it makes sense to routinely count high-value or fast-moving products each month. Other stock can be assessed quarterly. Real-time inventory insights are vital for driving visibility across your entire inventory management process and ensuring you’re equipped with the information needed to make data-backed decisions.
- Ensure products are counted for all SKUs listed.
- Determine the flow velocity of products, classifying items from fastest to slowest in relation to their movement through the warehouse. Consider automating this process to streamline workflow and productivity.
- Utilize analytics to monitor changes and make adjustments if needed.
- Ensure crews overseeing the counting process are well-versed in the practice.
- Use zero counts. This ensures warehouse workers are notified of an empty bin (typically caused by a picking order), so they can quickly verify that the bin is empty. By doing so, the facility can confirm that count completions of specific items were either correct or intervene if needed.
- Should an error crop up, always investigate the issue to eliminate it from recurring in the future.
- Documentation is key (we can’t stress this enough). From the process to changes made to the end result, capturing all the data will help reduce errors and promote consistency over time.
Leveraging Automation in Cycle Counting
Incorporating automation into the cycle counting process can bolster overall accuracy. Automation is also valuable because it boosts productivity, decreases labor costs, and enables real-time visibility into your inventory levels. In lieu of using messy and outdated manual spreadsheets, innovative technology, like inventory control software, gives your business the power to track inventory more efficiently — all while enjoying time and cost-saving benefits.At Smart Warehousing, we fuse together technology with decades of industry expertise to create a customized approach to inventory management based on your business’s unique needs. From our Smart Replenishment program, which helps stabilize inventory and meet consumer demand, to our cloud-based inventory management system, we can help manage your entire supply chain. Whether you need order fulfillment, logistics services, or inventory management, contact the Smart Warehousing team today to learn how we can help your business scale and thrive.
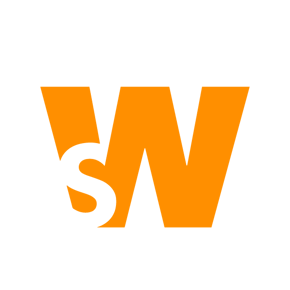