With many moving parts and essential steps to fulfill orders, it’s no wonder that fulfillment issues crop up from time to time! But if you can proactively mitigate the biggest pain points in your fulfillment process and establish effective solutions, these errors will become significantly less frequent (or vanish altogether!).
So what are the most common fulfillment issues, and how can you address them? Here are six common order fulfillment problems — and what your organization can do to prevent these shipping issues in the first place.
Problem: Poor Inventory Management
Many shipping issues and errors in the fulfillment process come down to ineffective inventory management. Inventory visibility in the warehouse is vital for supply chain efficiency and a positive customer experience. Lost inventory means lost profits, and running out of stock on popular items (or even ending up heavily overstocked!) can be equally damaging to your company’s financial stability, not to mention your brand’s reputation.
Solution: Efficient Inventory Management System
From replenishing stock in warehouses to shipping orders, an inventory management system that offers real-time visibility and cloud-based customer access can be the difference between satisfied customers and a flood of frustrated consumers. Inventory management software like SWIMS strategically stocks your inventory at locations near customers to create a seamless customer experience.
Outsourcing your inventory management to a third-party logistics provider (3PL) equipped with software that can also cover replenishment will ensure you never are without the inventory you need as orders come in, giving you up-to-date, relevant data based on proactive demand projections.
Problem: Shipping Issues
Though many shipping delays may occur due to poor inventory management, other complications in the delivery process may not even be warehouse related. Unfortunately, companies have little control over orders once products have left the warehouse in the hands of a last-mile carrier like UPS, USPS, or FedEx.
Solution: Decreased Distance
Strategically stocking inventory in warehouses near your customers will shorten the final leg of delivery and ease the burden on your last-mile carriers. When the last-mile carriers aren’t responsible for as much of the distance a product must travel to get to the customer, it’s easier for brands to guarantee rapid shipping times. (Bonus: It’s a cost-effective move too.)
A successful fulfillment process also depends on excellent relationships with last-mile carriers and being able to determine which carrier can best serve each individual order as it comes. Stocking your inventory and having heightened order visibility is not about distrust in last-mile carriers. On the contrary, it’s about partnerships to make sure shared customers remain happy and with their orders in hand on time!
Problem: Slow Picking and Packing
Heading back into the warehouse, picking and packing should never be slacking. Even with a high-visibility inventory management system, the pick-and-pack process can be slowed by warehouse mismanagement and human error.
Solution: Automated Warehouse Management
Automation is essential in the ever-evolving logistics space, and when automation is done well, it can cut out a lot of wasted time in the picking and packing process. The result? Fewer shipping issues! With real-time inventory visibility and accuracy, automated warehouse systems can quickly locate goods based on specific lots, batches, or serial numbers. This automated scanning and location tracking can also design a strategic warehouse management system that places fast-moving products toward the front of a warehouse, high-value products in a secure location, and so on.
Of course, automation alone is not enough! People are still vital to a fully operational and efficient warehouse, but automation can expedite processes and aid personnel in a seamless picking and packing process.
Problem: Incorrect Order Fulfillment
One of the worst fulfillment and shipping issues to tackle is sending a customer the wrong product. Now your company must decide whether to eat the cost of the product itself or pay for the customer to return it to you; either way, you’re coming out at a loss.
Wouldn’t it be better to avoid incorrect orders altogether? The solution to this fulfillment issue is — you guessed it — warehouse management!
Solution: End-to-End Order Fulfillment Coverage
Rather than managing order fulfillment internally, entrust the process to a 3PL that can guarantee efficient and accurate fulfillment! Whether you’re an e-commerce, retail, or B2B brand, the right 3PL will have systems in place to guarantee rapid, efficient, and accurate picking.
At Smart Warehousing, our robust warehouse management system can optimize your entire fulfillment process from start to finish to increase customer satisfaction and decrease your overhead.
Problem: Supply Chain Failures
Every consumer felt the impact of the supply chain issues in 2021, from ships full of inventory trapped at ports to worker shortages leaving trucks without drivers and warehouses full to the brim. The orders kept coming, but the inventory was stagnant! As a result, shipping issues were plentiful.
With the right warehousing strategy (paired with the right partner to keep the ball rolling), your supply chain can remain a seamless experience even in the midst of national shortages and crises.
Solution: A Localized Network of Warehouses
When you work with a 3PL, your inventory is out of your hands once you ship it to the warehouse. This puts a lot of responsibility on your 3PL to guarantee efficient supply chain processes, informing you of replenishment needs while keeping inventory moving throughout a network of warehouses localized to your customers.
The right network of warehouses can make all the difference when it comes to your supply chain, so your inventory will never get stuck in a single location. With Smart Warehousing’s network of 38 warehouses strategically spread throughout the United States, your inventory will never be left sitting in a port when customers are awaiting their orders!
Problem: Missing Orders
We’ve all been through this problem personally: you order something and received tracking details from the last-mile carrier, but suddenly your order disappears. No one seems to know where it is or how it got lost. What your order lacked was sufficient visibility.
This level of visibility is especially important for transporting perishable foods and cold chain inventory, where the time it has to get from the warehouse to the consumer is much more limited.
Solution: Increased Order Visibility
With real-time inventory visibility throughout the shelf life of your products (including when it’s in the hands of last-mile carriers), orders are kept in sight until they’re handed to the customer. Considering 91% of customers today expect order tracking visibility in real-time, it’s important for brands to trace their products throughout the entire fulfillment process. A 3PL that cares about efficiency and giving your customers the best possible experience should be able to provide this enhanced visibility, making product loss through missing orders a thing of the past.
Partner with a 3PL
With all this talk of visibility, let’s be completely transparent here: the solution to all your fulfillment woes and shipping issues is a full-service 3PL provider. Smart Warehousing has all of your fulfillment needs covered with design-thinking solutions that proactively track market trends and trends within your brand’s customers to guarantee an uninterrupted fulfillment experience.
Ready to enjoy the difference Smart Warehousing can offer your brand? Say hello to our fulfillment team and goodbye to fulfillment and shipping issues!
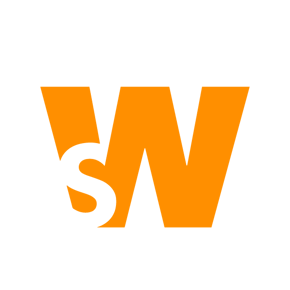