2021’s peak season is shaping up to be one of the busiest and one of the hardest to navigate. With labor shortages and capacity issues, businesses will need to make sure they have a game plan to deal with the upcoming challenges. With customer demands consistently increasing, making sure your supply chain is prepared will help you ensure customer satisfaction. 25% of shoppers say that efficiency in their shopping experience is a crucial factor when shopping for the holidays.
By taking the appropriate steps now and planning ahead you can avoid critical errors and ensure a seamless experience for your customers. With so many factors to consider during peak season, here are five fulfillment logistic mistakes you want to avoid.
Inventory Mismanagement
The biggest and some of the most problematic issues you can run into in fulfillment logistics begin with inventory issues. Mismanaging your inventory can lead to not having enough products and having to cancel customer orders and losing out on sales and possibly customers.
On the other hand, you could have way too much inventory and have to deal with the costs of storing and managing that overstock. Poor inventory management can escalate your business costs to accommodate the additional product. You may also have to sell the overstocked product at a discounted cost to help move it quicker, therefore affecting your bottom line even more.
In the fulfillment logistics world, it used to be a matter of having inventory ‘just in case,’ but with the new challenges facing the fulfillment industry, it has become a matter of having inventory just in time. As a business owner, you want to make sure you are using data from previous years to forecast your sales for this year. Use that data to help guide you on how much inventory to have consistently stocked and how often it will need to be replenished.
Not Planning Ahead
With the expected delays and shortages this holiday season, it’s more important than ever to plan ahead. This not only means planning your inventory but also organizing shipping, labor, and how you want to layout out your fulfillment process. If you are not planning properly, you could order inventory that you don’t have storage for. You could need to ship product out but if you don’t schedule with a carrier, you may be left scrambling to find a way to move it out of the warehouse.
Planning ahead also means looking at your entire fulfillment process and identifying where you might have some challenges or issues. Will you need to have your incoming shipments come to one part of your warehouse while outbound shipments stay in a separate location? Will you need to schedule your workers on certain days for certain hours to make sure orders are fulfilled? In the fulfillment logistics world, planning ahead could help you as a business owner avoid panic within the business.
Slow Shipping
One of the most important parts of fulfillment logistics is how quickly you can get your product to your customer. In fact, 36% of digital shoppers abandon their carts because the item will take forever to ship. With shipping speed being such a critical factor, it should be a top priority for business owners. Shipping carriers are already struggling and with more pressure expected as peak season gears up, businesses could see delays increase.
Not planning your shipments can lead to delays in the shipment, ultimately impacting customer satisfaction. In an Oracle survey, 80% of responders said they would stop buying from a brand after one to three delays or disruptions. If you don’t have relationships with carriers, now may be the time to start curating some. If you already do, you will want to be in contact with them to make sure your shipments are being picked up.
Not Optimizing Your Network
A straightforward way to avoid issues during peak season is by making sure your fulfillment center and your processes are optimized as much as possible. In the fulfillment logistics world, optimization can save you a ton of time and help your fulfillment process run seamlessly. If you don’t look at the big picture and what changes you can make to help optimize your fulfillment process, you may see higher costs and longer delays.
One way to optimize is by thinking about how you organize your fulfillment center or warehouse. If you have a few popular products, put those upfront right by your packaging center so workers don’t have to travel far to fulfill their orders. You can place popular products in easy-to-reach places to make sure your workers can quickly pick the item. Quicker picking can help you fulfill more orders faster, allowing you to get orders out quicker and cut down on labor costs.
If you have multiple fulfillment centers across the country, you can utilize those to disperse your inventory, putting it closer to customers. If you spread your inventory across multiple fulfillment centers, you can ship the product from the center closest to the customer. This will help cut down on both costs and shipping time, which will improve your customer experience.
Outdated Technology
Fulfillment technology has come a long way in the last decade, allowing you to see inventory levels whenever you want. But if you’re not updating your technology or are using slow or unreliable systems, you could be hurting your business. So much of fulfillment logistics relies on technology and not having the ability to integrate or share information can hamper you.
Outdated technology can lead to several issues. For instance, if your technology does not consistently update your inventory levels, you may not know a product is out of stock, leading to issues when a customer orders the product. It may also tell your pickers an incorrect location for the product so when they go to pick the item it is no longer there.
If your technology is outdated, it may not be compatible with the technology your vendors use and could lead to issues sharing and receiving information. This may mean not being able to integrate with certain platforms or having to share information manually.
Pick The Right Fulfillment Logistics Partner
With all the challenges this peak season will present, finding the right fulfillment logistics partner can be vital to your success. A good fulfillment logistics partner can help make sure you have the right inventory at the right place at the right time. They can help you with making sure you have your shipping needs met and that you are optimizing your fulfillment process.
This is where Smart Warehousing comes in. Smart Warehousing is a full-service fulfillment partner. We can provide full supply chain solutions to you and help you tackle these issues. With a network of 30+ warehouses nationwide, we can get your inventory where it needs to be when it needs to be there. Don’t wait until the issues arise — tackle them now by picking a fulfillment logistics partner that can help you prevent them. Contact us today to learn more.
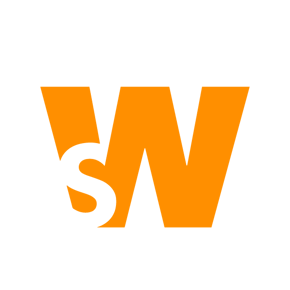