While luck has a little something to do with it, successful business outcomes are nearly always the result of intentional, smart strategy. From finance to marketing and everything in between, success can’t be expected if you leave things to chance. And the same logic applies to your supply chain management strategy. From the order fulfillment process to product shipment, how can you expect to scale and fuel profitability with no visibility or cohesive strategy in place? From startups to household-name enterprises, strategy is everything.
Leveraging a technology-driven warehouse management system (WMS) is an imperative part of driving operational efficiency and output across your supply chain. A warehouse management system allows you to monitor and streamline processes across various stages of a product’s lifecycle, decreasing error and improving the customer experience. What’s more, it can help optimize inventory management by using data to expertly balance supply and demand.
A strong WMS is fundamental to ensuring your supply chain management practices are carried out seamlessly and successfully. Here’s a look at the features and benefits of having the right warehouse management system on your side.
1. Decreased Operating Expenses and Optimized Space
Top-notch warehouse management systems can analyze inventory and floor space to identify valuable waste reduction opportunities and optimize ideal product flow. By doing so, your organization can decrease costs associated with time-consuming retrieval and excessive material movement. From how products are stored to materials or equipment needed, a WMS can determine the most effective solution for your unique supply chain management needs, resulting in lower operating expenses.
WMS solutions can also manage the physical movement of merchandise as it is brought into, and shipped out of, the warehouse. For instance, the first-in, first-out (FIFO) rotation rule is often used to preserve product quality and integrity — especially for temperature-sensitive items and perishables like meat, dairy, pharmaceuticals, cosmetics and more. The ideal warehouse management system is designed with flexibility and versatility in mind, facilitating processes in a manner that aligns with a company’s specific business objectives and consumer demand.
2. Real-Time Inventory Visibility
Inventory visibility and accuracy are at the heart of an effective supply chain management strategy. Because the unfortunate reality is, erroneous stock records can do some serious damage to your revenue flow, margin, and company reputation. Minimizing transaction error rates (and earning customer loyalty!) through reliable product delivery is a crucial part of running a successful business and scaling up to new heights.
A few hiccups may seem trivial in the grand scheme of things, but online reviews and social media platforms are powerful tools for disgruntled customers to vent about their less-than-stellar experiences. Social proof matters.
The stats speak for themselves. When your business has positive reviews, 31% more money is spent by customers. On the flip side, businesses can lose as many as 22% of customers considering purchasing their product due to one negative article. And that number jumps to 59.2% if there are three people shouting from the rooftops about their negative experiences.
The bottom line: a robust warehouse management system with real-time inventory insights can directly impact sales — from uncovering discrepancies in inventory levels and meeting customer demand to establishing sales trends and avoiding backorders.
A strong WMS will also be able to integrate with ERP systems to streamline processes, document product performance, and forecast future demands. This allows leaders to make supply chain management adjustments based on reporting data to mitigate losses and increase revenue.
3. Product Tracking and Transparency
Automated scanning and location tracking capabilities provided by a warehouse management system will ensure inventory is accounted for and not lost or accidentally misplaced. Goods can be traced via lot, batch, and serial numbering, to identify individual items as well as groups of inventory based on their classification — i.e. high-value products, fast-moving products, and so on.
A quality inventory tracking system provides full traceability, allowing users to match specific serial or batch numbers with outgoing shipments and order receipts. Being able to trace goods at any given point in time decreases potential redundancy, promotes accurate inventory planning, and enables the end-user to retrieve vital information for recall scenarios and service maintenance.
And on a forward-focused scale, the tracking metrics help for future planning, so you can stay on top of shopper trends and be sure inventory is ready when demand hits. The Pandemic delivered countless case studies on how crucial it is for companies to be nimble and agile. Because of the Pandemic, 28% of retailers underwent shortages and out-of-stocks, and 64% were challenged to adapt their supply chain management. An effective warehouse management system can ensure you’re ready to pivot when needed.
4. An Optimized Supply Chain
When the entire fulfillment process, from initial order to outbound delivery, is streamlined and managed via a warehouse management system, it will naturally improve operational efficiency and decrease overhead costs. Effective software will significantly reduce redundant or unproductive activities, which in turn strengthens workflow and allows your staff to focus their time on more high-level, revenue-generating initiatives.
For instance, when order fulfillment and inventory management are aligned, it benefits all parties involved: suppliers, shippers, customers, and your team. Why? Because an optimized supply chain trims the fat from operations while reducing inventory costs and enabling faster delivery time.
What’s more, a warehouse management system can reduce manual error and help ensure records are filed electronically in lieu of messy, outdated paperwork. It also encourages process improvement from a strategic standpoint, as data captured can be used to evaluate what’s working, what’s not working, and what you can potentially capitalize on within your supply chain management.
When information is accurate and easily accessible, it gives companies the bandwidth to successfully scale – whether that’s in the form of expanding into new markets, launching new products, or targeting a new consumer base.
5. Improved Shipping & Customer Service
Both inbound and outbound procedures can be managed with the right warehouse management solution. The date and time of an inventory shipment to a warehouse can be optimized by taking equipment and labor availability into consideration. This fosters planning and preparation at both the receiving end of the equation, as well as outbound shipping.
For instance, picking and packing products can be executed in a manner that eliminates any holdups or delays to accelerate the customer order cycle and improve the consumer experience. Today’s consumers not only want their products to arrive quickly (thanks, Amazon), but they also want to receive the correct order. Shocking, we know. If a customer receives the wrong item or the wrong number of items, you’ll essentially be handing them over to your competitors, gift-wrapped with a bow on top. So timing and accuracy are crucial pieces of the equation.
Expertise and Technology, Tailored Just for You
Finding a warehouse management system that alleviates error and maximizes profitability will drive long-term success for your organization. The goal is to partner with a 3PL provider that has the know-how and technology in place to simplify the otherwise complex supply chain process.
At Smart Warehousing, our cloud-based Smart Warehousing Information Management System (aka, SWIMS) was designed to move the needle forward for your business. From real-time inventory insights to the ability to integrate with your tech stack, our goal is to develop a customized program to accommodate your individual business needs. Our experts can oversee everything from order fulfillment to inventory management to logistics, helping you meet demand and achieve growth.
Contact the Smart Warehousing team today to learn more about how we can deliver a solution that’ll help your business thrive.
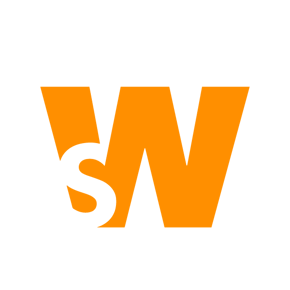